Thermochemische Nitrierverfahren
In der Industrie werden drei gängige Nitrierverfahren verwendet. Die gewählte Methode hängt von der jeweiligen Anwendung der nitrierten Komponenten ab.
Im Folgenden werden die Nitrierverfahren kurz beschrieben. Eine ausführliche Beschreibung der Prozesse und deren Einfluss auf die Eigenschaften der nitrierten Komponenten und Teile ist der vollständigen Application Note zu entnehmen, die
hier heruntergeladen wird. Nitrocarburieren im Salzbad Nach dem Vorwärmen werden die Komponenten in ein Salzbad aus alkalischem Cyanat und alkalischem Carbonat getaucht. Durch Oxidation und thermische Reaktion setzt das alkalische Cyanat Stickstoff und Kohlenstoff frei, die in die Oberfläche des Metalls diffundieren.
Nach dem Carbonitrieren im Salzbad wird die Komponente in einem oxidierenden Salzbad abgeschreckt. Dadurch entsteht schwarzes Eisenoxid (Fe
3O
4), das die Poren der Verbindungsschicht füllt und zusätzlichen Korrosionsschutz bietet.
- Typische Anwendungen: Teile für die Automobilindustrie wie Kolbenstangen, Nockenwellen und Zahnräder sowie Teile für die Luftfahrt-, Offshore- und Maschinenbauindustrie.
Gasnitrieren und Gasnitrocarburieren Beim Gasnitrieren wird die Komponente in einen geschlossenen, Haubennitrierofen gestellt. Sobald die Nitriertemperatur erreicht ist, wird Ammoniak in den Ofen geleitet. Bei der Reaktion von Ammoniak mit dem Metall wird ersteres zersetzt und setzt Stickstoff frei, der in die Metalloberfläche diffundiert. Durch Zusatz kohlenstoffhaltiger Gase kann auch im Gas nitrocarburiert werden.
- Typische Anwendungen: Maschinenspindeln, Gußeisen-Pumpengehäuse, Türverriegelungen, Wasserpumpenkomponenten und Kolben für Gaskompressoren.
Plasmanitrieren und Plasmanitrocarburieren Das Plasmanitrieren erfolgt in Stickstoff/Wasserstoff-Atmosphäre. Das Plasma wird in einer Vakuumkammer mit hoher Spannung hergestellt. In dieser Umgebung dient die Metallkomponente als Kathode und das Vakuumgefäß als Anode. Der Prozess des Plasmanitrocarburierens gleicht dem des Plasmanitrieren, es werden allerdings kohlenstoffhaltige Gase eingeleitet.
- Typische Anwendungen: Da das Plasmanitrieren eine Vielzahl von Nitridschichten ermöglicht, können die Komponenten in einer Vielfalt von Anwendungen eingesetzt werden. Dazu gehören Nockenwellen und Kurbelwellen in Hochleistungsmotoren, Maschinenspindeln, Autokarosserie-Stanzen, korrosionsbeständige Motorventile und Zerspanungswerkzeuge aus HSS-Stahl.
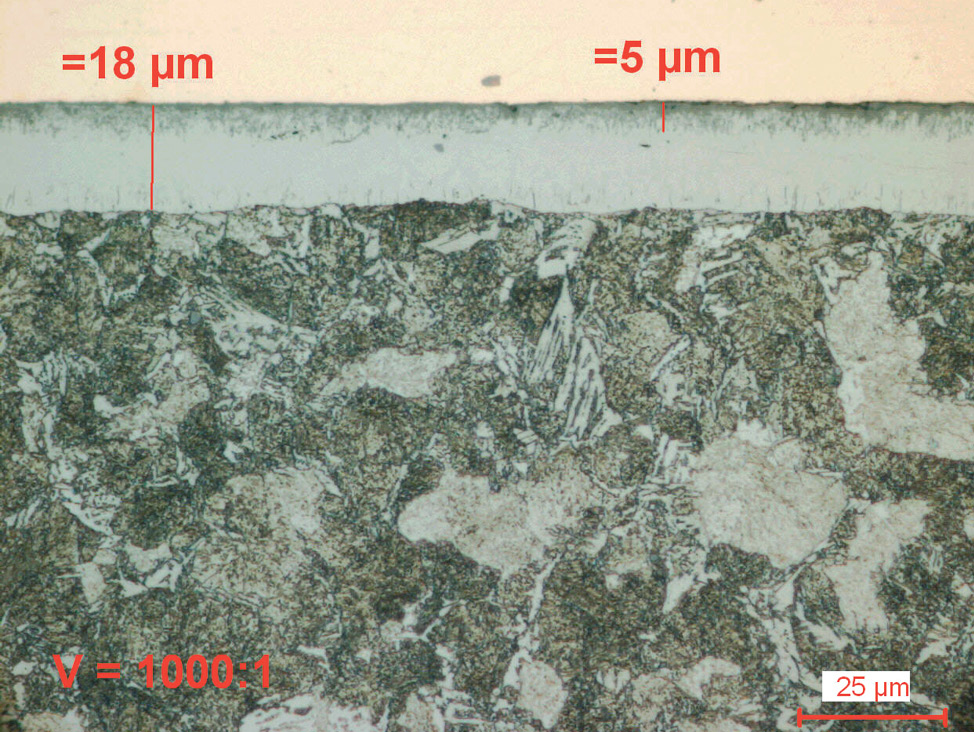
Abb. 4:
Stahllegierung (16MnCr5), carbonitriert im Salzbad, geätzt mit 1 % Nital. Die Diffusionszone ist dunkel geätzt und die Verbindungsschicht mit der porösen Zone ist weiß.
Abb. 5: Gasnitrocarburierter Kohlenstoffstahl (580 °C über 1,5 Stunden).
Abb. 6: Plasmacarbonitrierter Kohlenstoffstahl (570 °C über 6 Stunden). Beide Nitridschichten weisen keine poröse Zone, aber eine sehr feine Oberflächegüte auf.