Información sobre aleaciones
En la actualidad, los materiales utilizados en aplicaciones prácticas son una mezcla de varios elementos químicos conocida como "aleaciones". El acero y el hierro fundido, por ejemplo, son aleaciones esenciales basadas en hierro (Fe) con adición de carbono (C), el cual es responsable de la dureza del material férreo. El análisis microestructural nos permite conocer las propiedades de la aleación, tales como su resistencia, dureza y ductilidad.
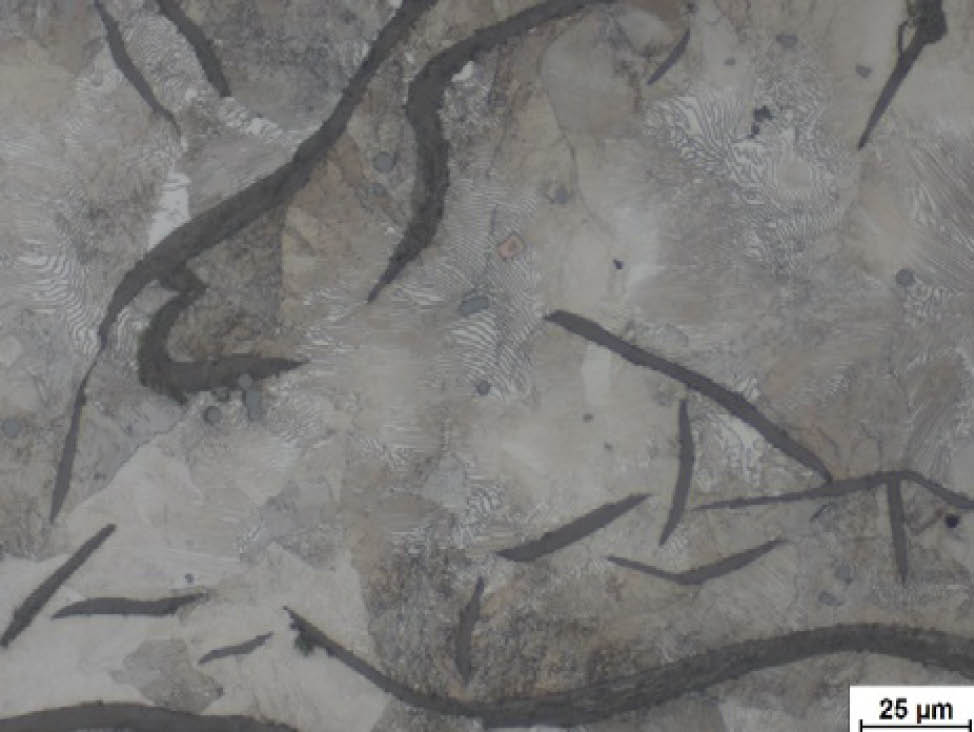
Fig. 3: Hierro fundido perlítico con grafito laminar, sometido a ataque químico con Nital. El carbono está presente como grafito en forma laminar, lo cual reduce su resistencia. La matriz perlítica en sí ofrece un nivel suficientemente alto de dureza.
Imagen tomada con microscopio Axio de ZEISS, objetivo 50x, iluminación de campo claro (BF)
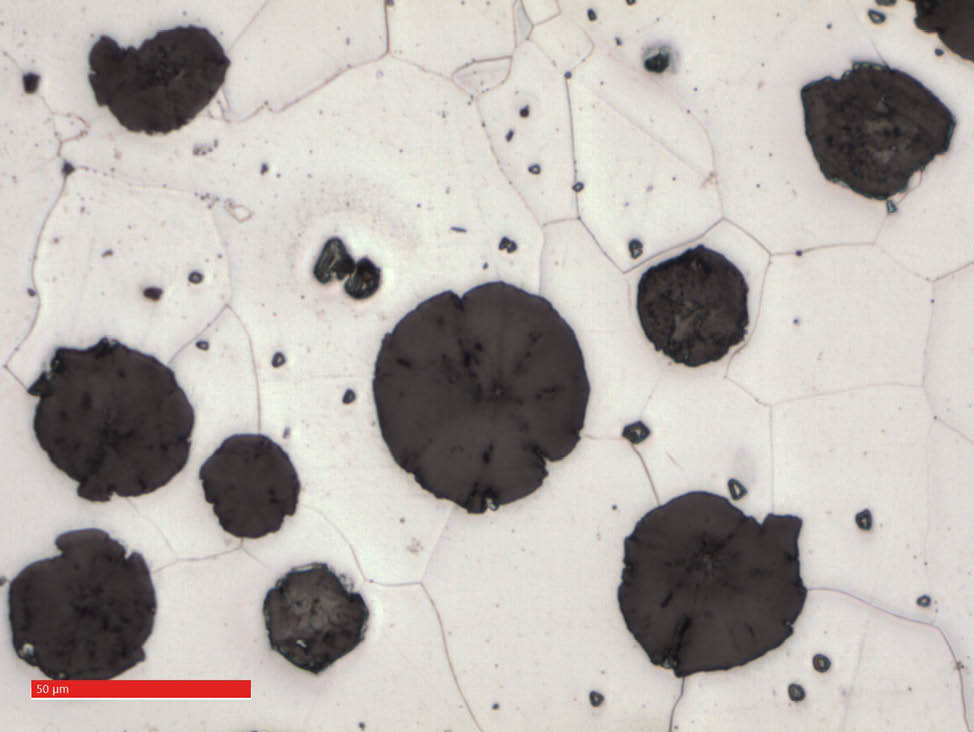
Fig. 4: Hierro fundido ferrítico con grafito esferoidal, sometido a ataque químico con Nital. El carbono está presente como grafito en forma esferoidal. Dicha forma esferoidal mejora la resistencia respecto al hierro fundido en forma laminar, aunque la dureza del material es inferior debido a la falta de cementita en la matriz ferrítica.
Imagen tomada con microscopio digital Smartzoom 5 de ZEISS, con ampliación aproximada de 500x
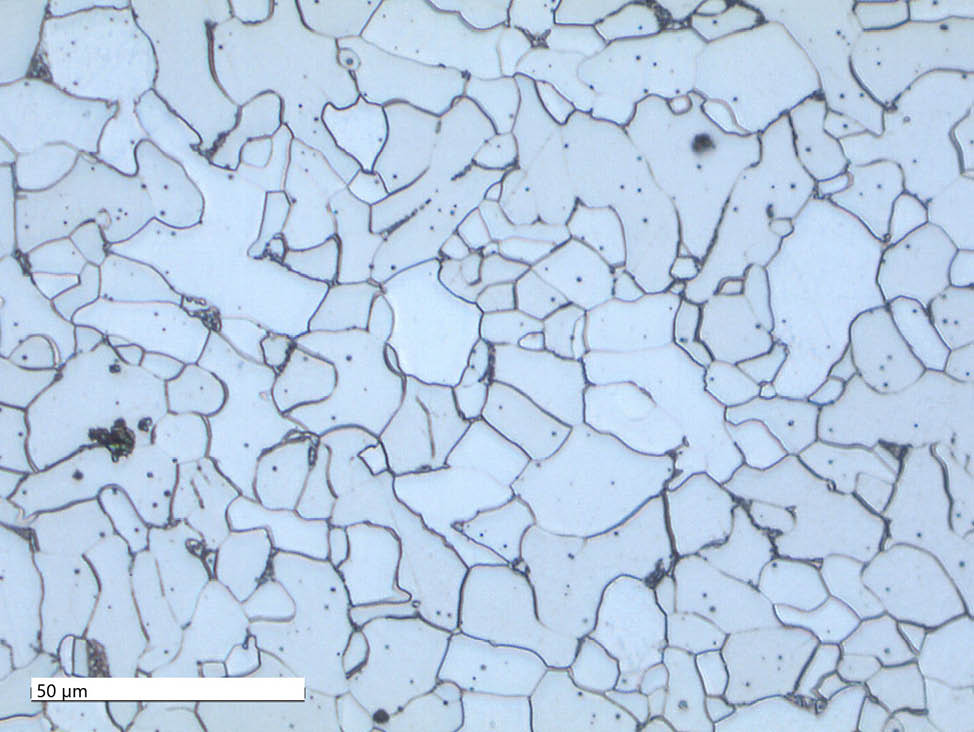
Fig. 5: Acero ferrítico con aproximadamente 0,1 % de carbono, sometido a ataque químico con Nital. El carbono está presente en forma de cementita y en baja proporción de perlita entre los granos ferríticos. La matriz, que es en gran medida ferrítica, ofrece un grado bajo de dureza pero gran ductilidad.
Imagen tomada con microscopio digital Smartzoom 5 de ZEISS con ampliación aproximada de 500x, iluminación coaxial con baja proporción de luz anular
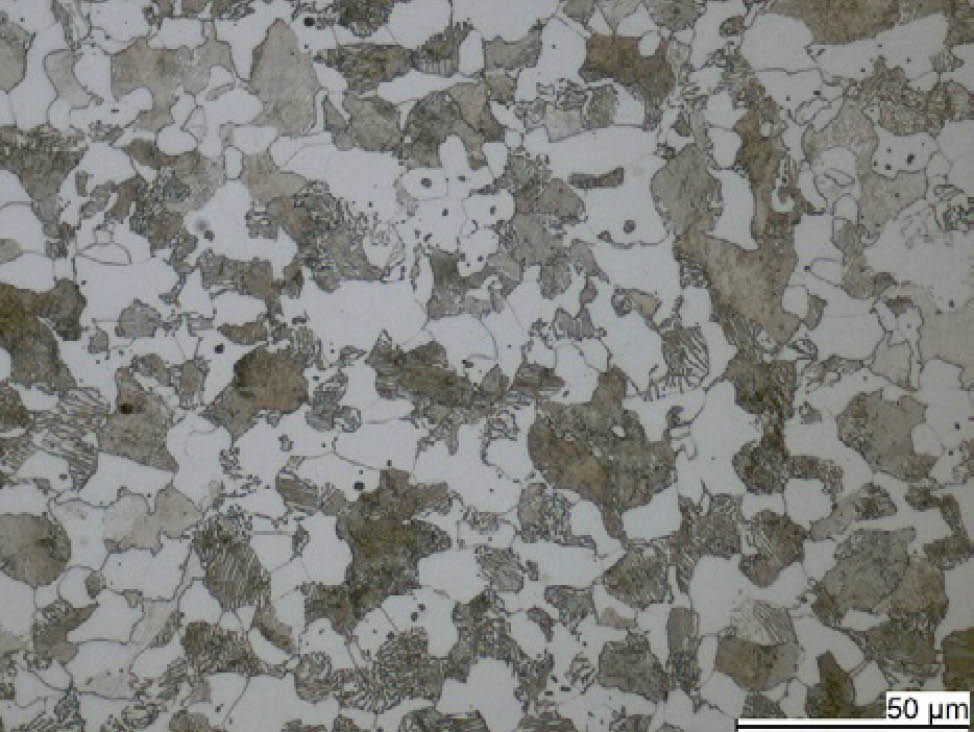
Fig. 6: Acero ferrítico-perlítico con aprox. 0,2 % de carbono, sometido a ataque químico con Nital. El carbono está presente como cementita laminar y en baja proporción de perlita adyacente a los granos ferríticos. Esto hace que la cementita se muestre en forma estriada. Los granos perlíticos reflejan menos luz que los ferríticos y por lo tanto se muestran más oscuros. Una matriz de este tipo tiene mayor dureza, pero menor ductilidad.
Imagen tomada con microscopio Axiolab de ZEISS, objetivo 50x, iluminación de campo claro (BF)