Retos de la preparación de muestras microelectrónicas
Existen tres retos principales al realizar un control de eliminación de material y la preparación del objetivo en las muestras microelectrónicas.
Las dimensiones diminutas requieren equipos especializados y accesorios adecuados para el manejo de muestras pequeñas. Pasos como el corte y el esmerilado requieren mayor precisión de lo normal, debido a las dimensiones, que normalmente se encuentran en un rango de µm.
La composición compleja del material es algo común en microelectrónica donde metales blandos, cerámica y compuestos a menudo se encuentran en una misma pieza. Esto compromete la elección de los métodos de preparación y los parámetros, seleccionados cuidadosamente para cumplir los requisitos específicos.
El control de eliminación de material y su preparación precisa es esencial cuando los objetivos pequeños se someten a examen. Una inspección metalográfica de la muestra a menudo incluye la búsqueda de un área concreta en el interior del encapsulado de chips interconectados. Esto puede requerir mucho tiempo, ya que normalmente implica un control de eliminación de material manual conocido como "esmerilado y observación" (i.e. esmerilado reiterado y posterior comprobación del objetivo hasta que esté listo para el pulido).
En investigación o análisis de fallos, la pérdida del objetivo durante el proceso de "esmerilado y observación" puede suponer la pérdida de una muestra única y/o costosa. Por lo tanto, las soluciones automatizadas u optimizadas se utilizan con gran frecuencia debido a su alta precisión mecánica, unidades de medición óptima y paradas mecánicas.
Las dificultades más habituales en la preparación de elementos microelectrónicos son:
- El corte: Desconchado y fractura de obleas de silicio, cristal o cerámica
- La embutición: Deformación mecánica y daños térmicos
- El esmerilado: Fractura de componentes quebradizos como fibras de cristal o cerámica
- El pulido: Aparición de manchas en capas del metal blando; relieve debido a la variación de dureza de los distintos materiales; carburo de silicio y partículas de diamante restantes en la soldadura
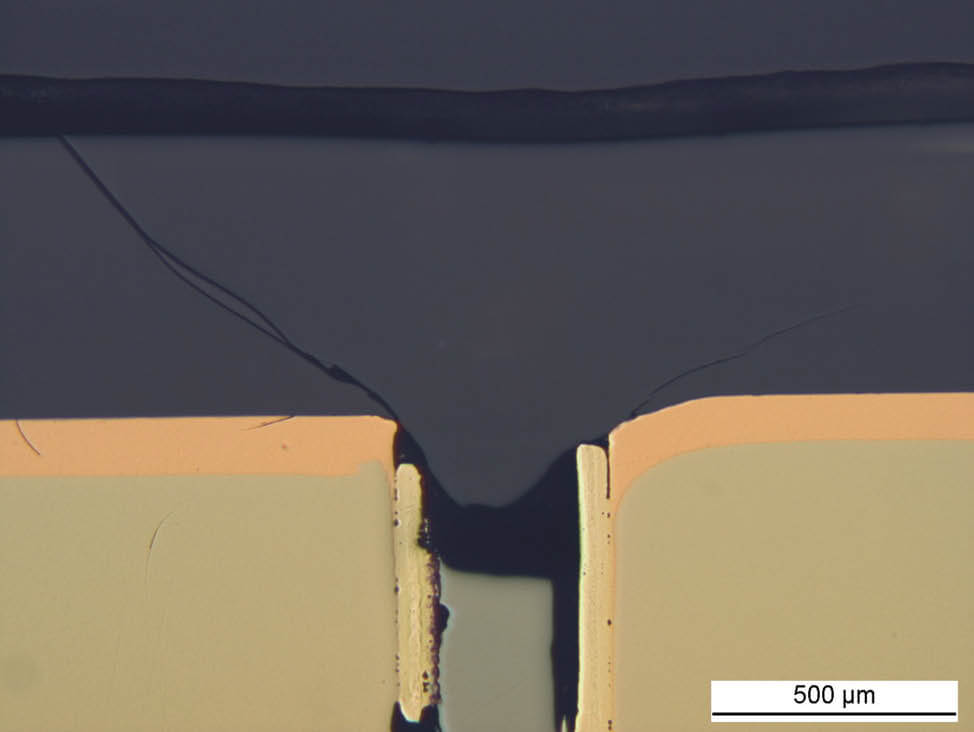
Fig. 7: Detección de una fractura en un diodo
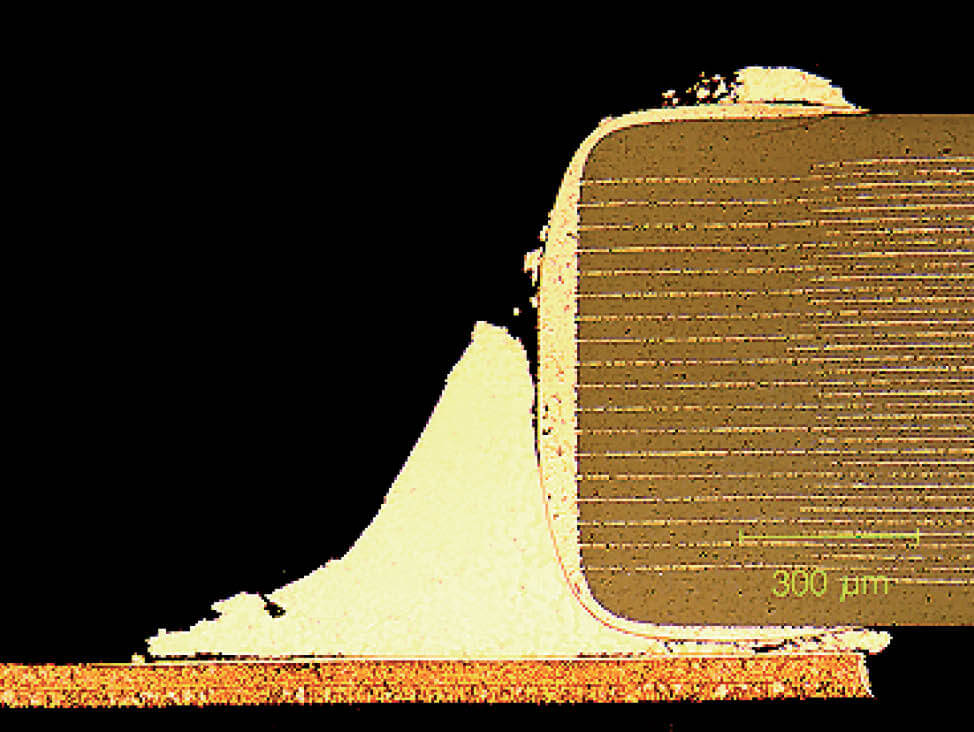
Fig. 8: Sección en condensador cerámico multicapa envejecido con fracturas de fatiga en la conexión soldada
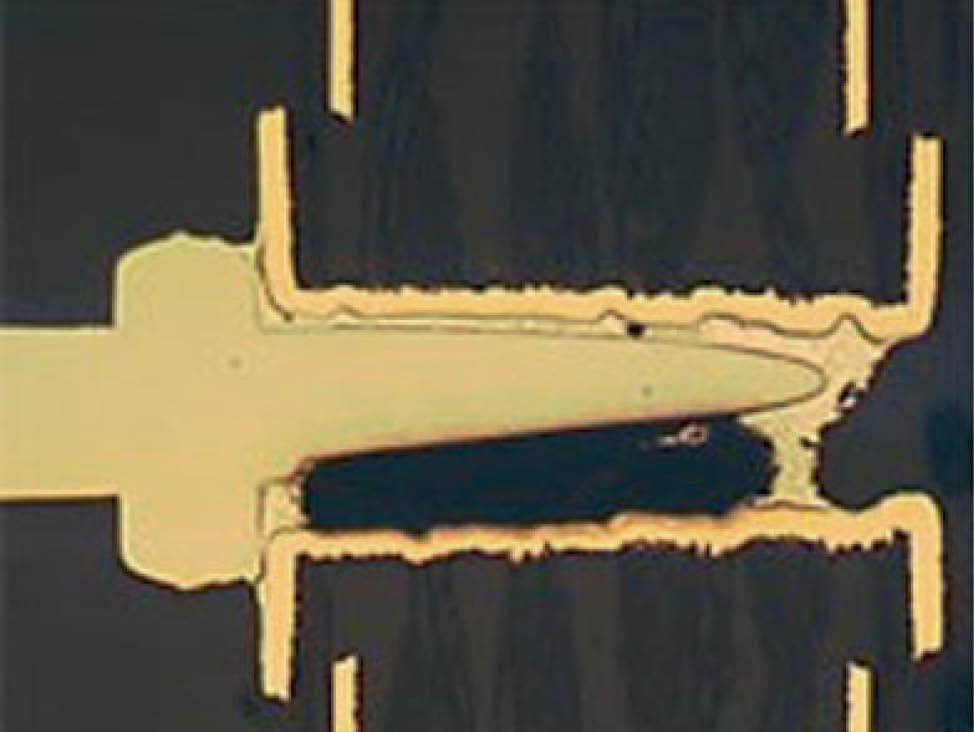
Fig. 9: Gran hueco en la conexión del agujero pasante metalizado (50 aumentos)
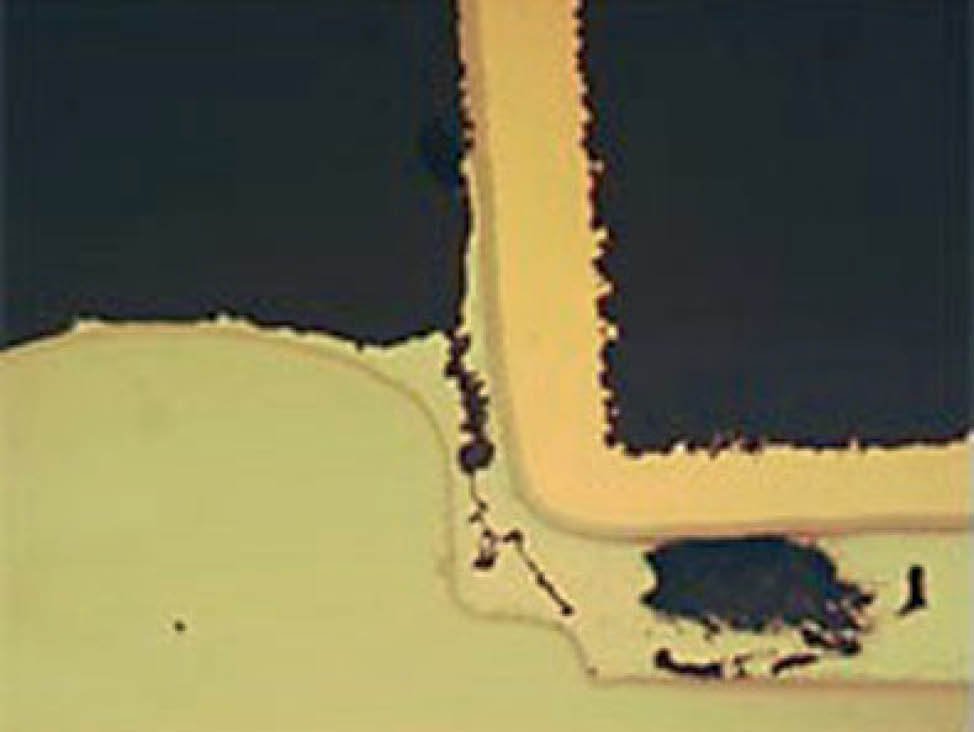
Fig. 10: Hueco y fractura en la conexión de soldadura del agujero pasante metalizado (200 aumentos)
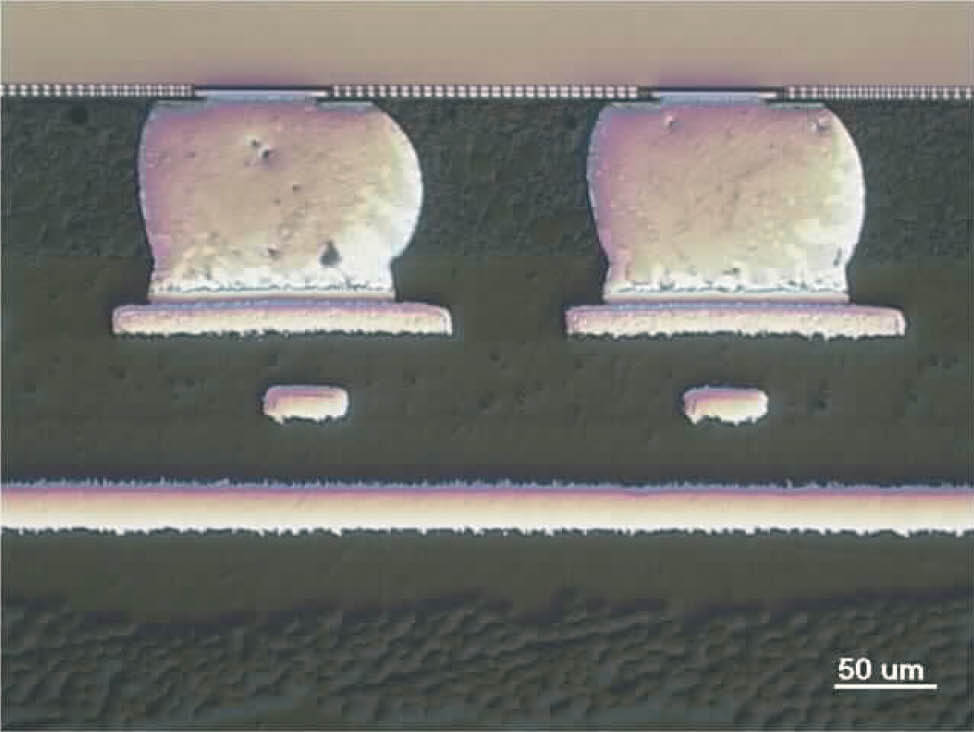
Fig. 11: Sección transversal de esferas de soldadura, DIC (Contraste Diferencial de Interferencia)