Les défis de la préparation d’échantillons de composants microélectroniques
L’enlèvement contrôlé de matière et la préparation des cibles d’échantillons de composants microélectroniques comportent trois défis principaux.
Les dimensions minimales nécessitent des équipements et accessoires spéciaux, adaptés au traitement de petits échantillons. Les étapes telles que le tronçonnage et le prépolissage exigent une précision supérieure, à cause des dimensions des échantillons, généralement de l’ordre du µm.
Les composants microélectroniques présentent fréquemment des
assemblages complexes, dans lesquels des métaux tendres, de la céramique et des composites sont souvent étroitement assemblés. Le choix des méthodes et paramètres de préparation est dès lors un compromis, qui doit être sélectionné avec soin pour répondre à des exigences spécifiques.
Un enlèvement de matière contrôlé et une préparation minutieuse sont indispensables lorsque les cibles examinées sont de petite taille. L’inspection d’un échantillon métallographique consiste souvent à observer une zone particulière à l’intérieur d’un ensemble de puces interconnectées. Cette procédure peut demander du temps, car elle repose généralement sur un processus manuel d’enlèvement de matière contrôlé appelé « prépolissage et examen » consistant à prépolir, puis examiner l’échantillon jusqu’à ce que la cible apparaisse et soit prête à être polie.
Lors de la recherche ou l’analyse des défauts, manquer la cible pendant un processus de « prépolissage et examen » peut entraîner la perte d’un échantillon unique et/ou coûteux. C’est pourquoi les solutions automatisées ou optimisées sont de plus en plus souvent privilégiées pour leur précision mécanique supérieure, leurs équipements de mesure optiques et leurs butées mécaniques.
Parmi les difficultés courantes lors de la préparation d’échantillons de composants microélectroniques figurent notamment /
- Tronçonnage : Écaillage et fissuration des wafers en silicium, du verre ou de la céramique
- Enrobage : Déformation mécanique et dommages thermiques
- Prépolissage : Fracturation des constituants fragiles tels que les fibres de verre ou la céramique
- Polissage : Beurrage des couches de métaux tendres ; reliefs dus à la différence de dureté de différents matériaux ; incrustation de particules de carbure de silicium et de diamant dans la soudure
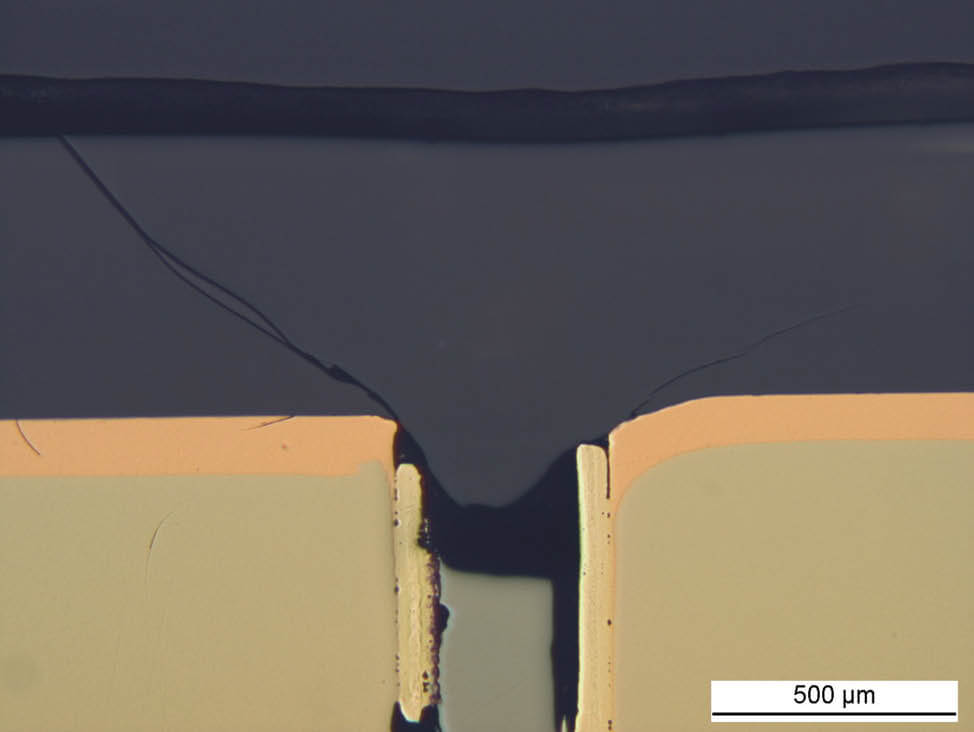
Fig. 7: Détection d’une fissure dans une diode
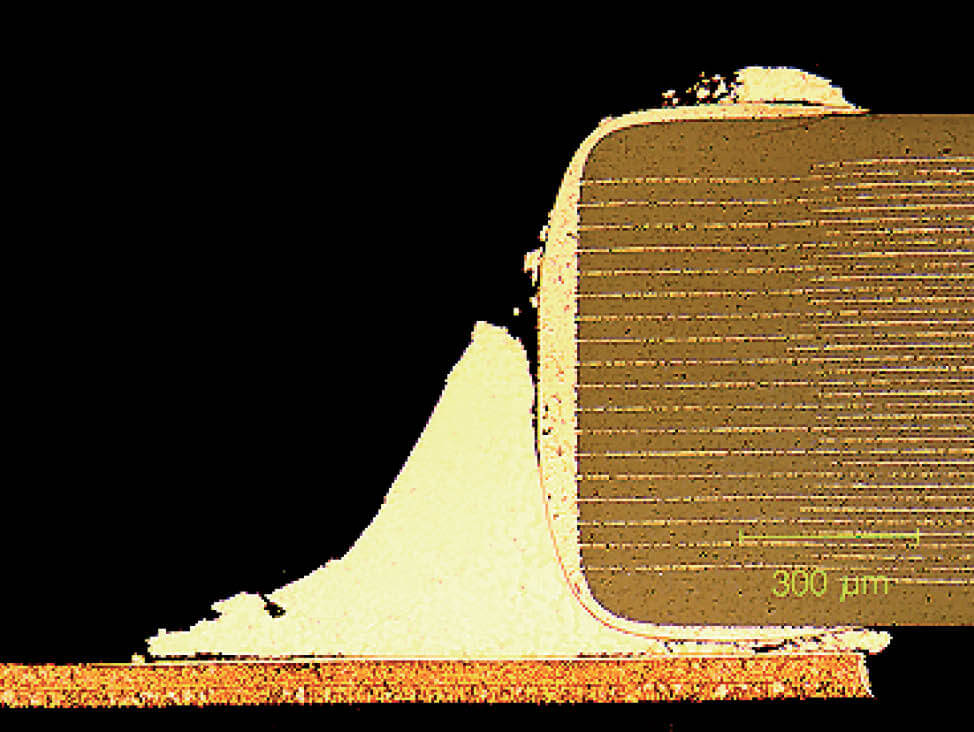
Fig. 8 : Coupe d’un condensateur céramique multicouche usagé avec présence de fissures de fatigue dans la connexion soudée
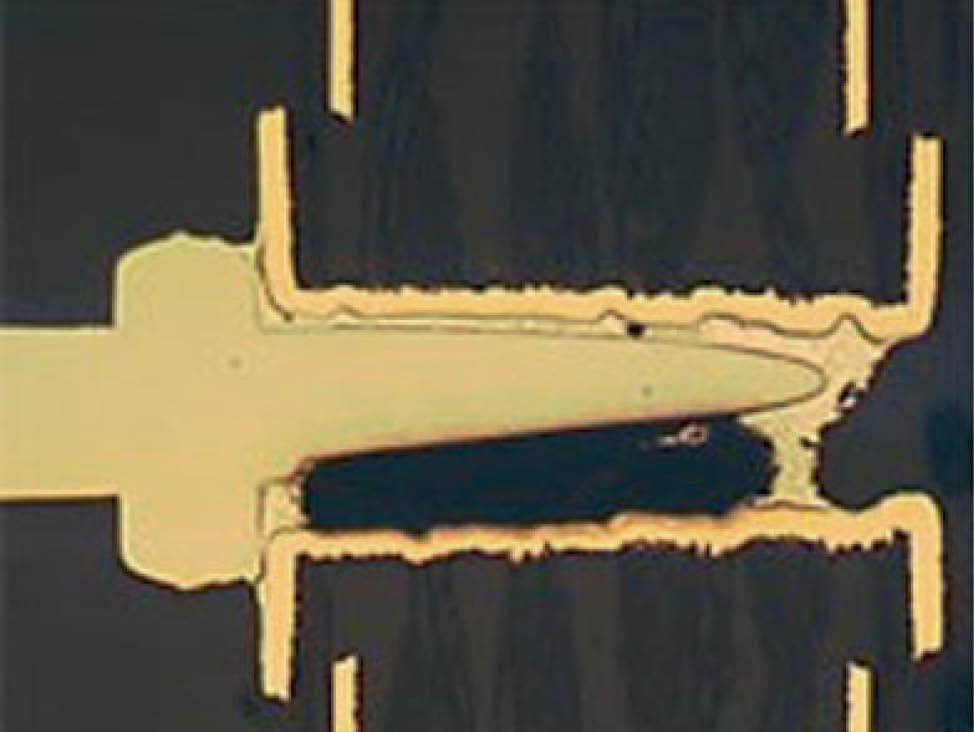
Fig. 9 : Grand vide dans la soudure d’une connexion à trou traversant métallisé (50 x)
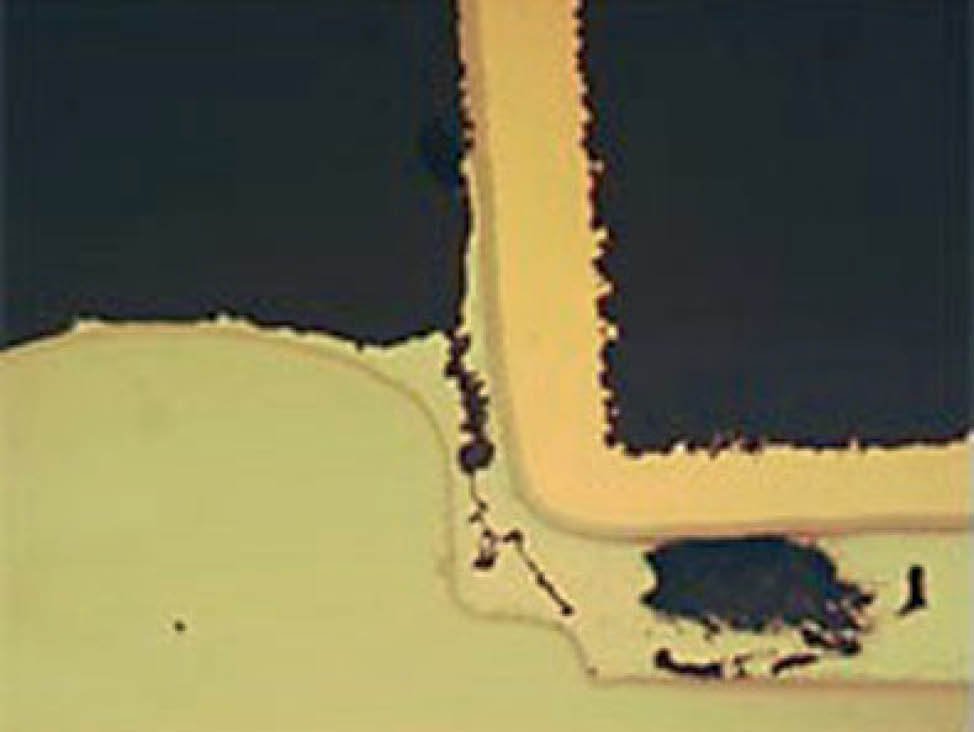
Fig. 10 : Vide et fissure dans la connexion soudée d’un trou traversant métallisé (200 x)
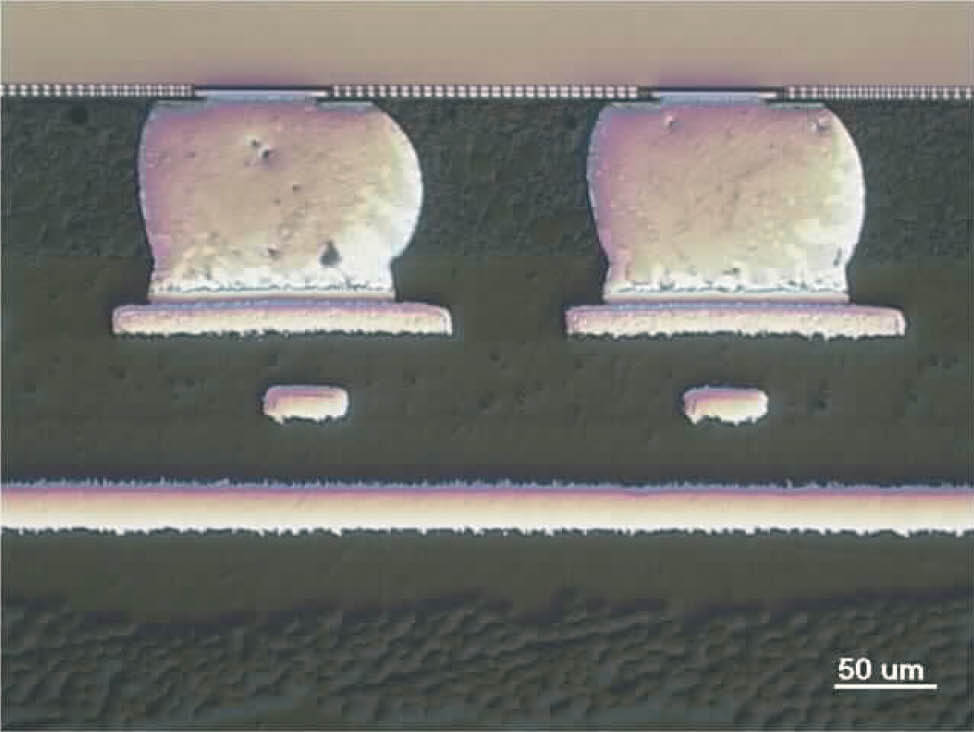
Fig.11 : Coupe transversale de billes de soudure, contraste interférentiel