Challenges when preparing zinc coatings for metallographic analysis
As zinc coatings vary in hardness and thickness, they behave differently during metallographic preparation. In addition, some zinc coatings react with water, which makes preparation particularly challenging.
Challenges during mounting
Mounting of zinc coated specimens can be a challenge, especially when time is an issue. To avoid shrinkage gaps, proper adhesion between the mounting material and the specimen must be ensured.
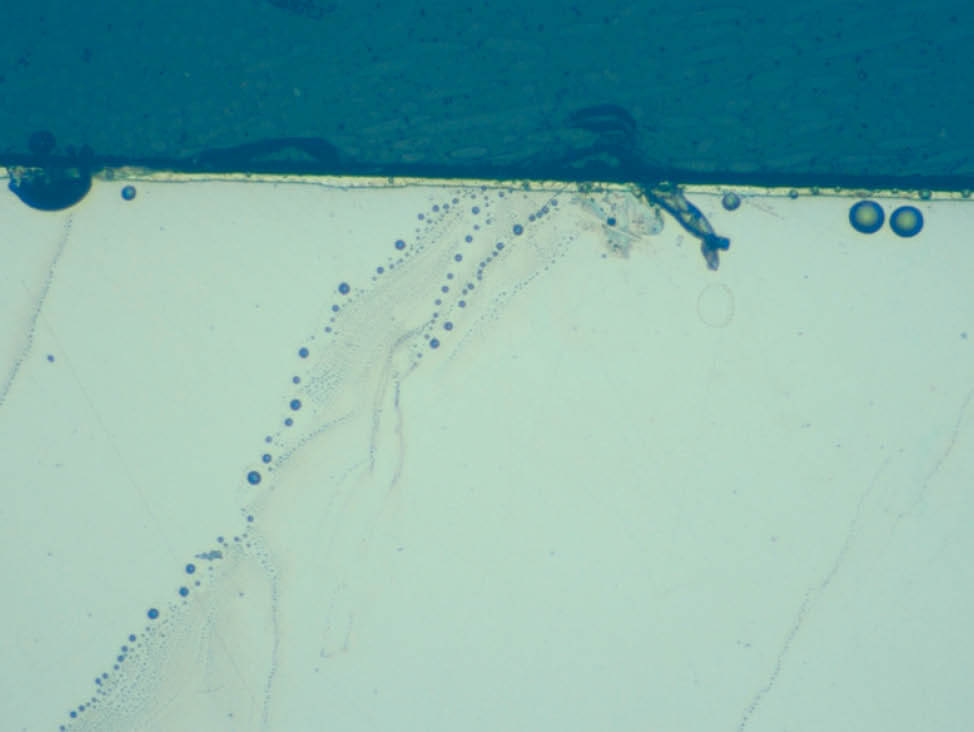
Fig. 6: Shrinkage gaps between the specimen and resin can cause water and alcohol stains, as well as edge rounding and trapped grinding debris, 200x
Challenges during grinding and polishing steps
Zinc coatings become softer and more water sensitive depending on the purity of the zinc in the coating, especially plain hot dip and electrolytically deposited coatings, which have a high zinc content. This makes them soft and prone to mechanical deformation. They cannot be cleaned with water.
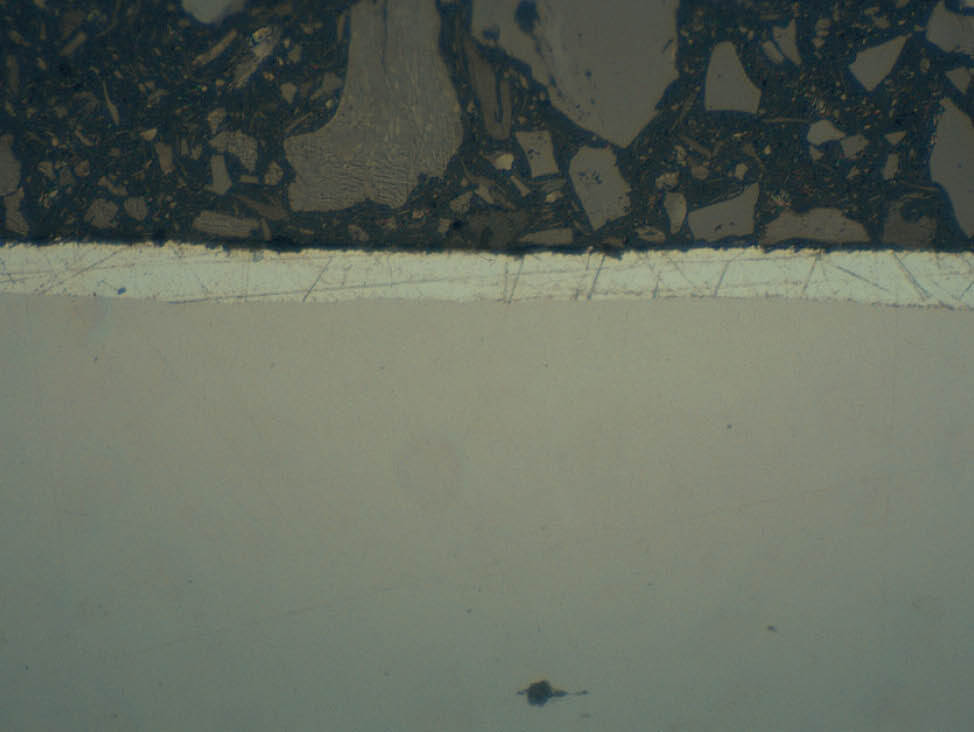
Fig. 7: Soft coatings, visible scratches from grinding and polishing steps, 500x

Fig. 8: The reaction with water leads to discoloration and zinc attack, 1000x