Schleifen, Polieren und Ätzen von additiv gefertigten Teilen
Bei der Arbeit mit additiv gefertigten Proben variieren die Präparationsschritte Schleifen, Polieren und Ätzen je nach Material/Legierung stark. Hier sind kurze Empfehlungen für vier gängige Materialien, die in AM verwendet werden.
Titan In der Regel sollte die Präparation den Standardmethoden folgen, die für andere Titanproben verwendet werden.
- Titan neigt aufgrund seiner hohen Duktilität zu mechanischer Verformung und Kratzerbildung. Diamantpolieren sollte insbesondere bei Reintitan vermieden werden.
- Bei niedriglegiertem Titan wird das Elektropolieren empfohlen.
- Um weitere Informationen zu erhalten, ist nach der mechanischen oder elektrolytischen Präparation häufig ein Ätzen erforderlich. Da Titan chemisch beständig ist, werden flusssäurehaltige Ätzmitteln empfohlen.
- Polarisiertes Licht ist eine ausgezeichnete optische Ätzmethode für Titan.
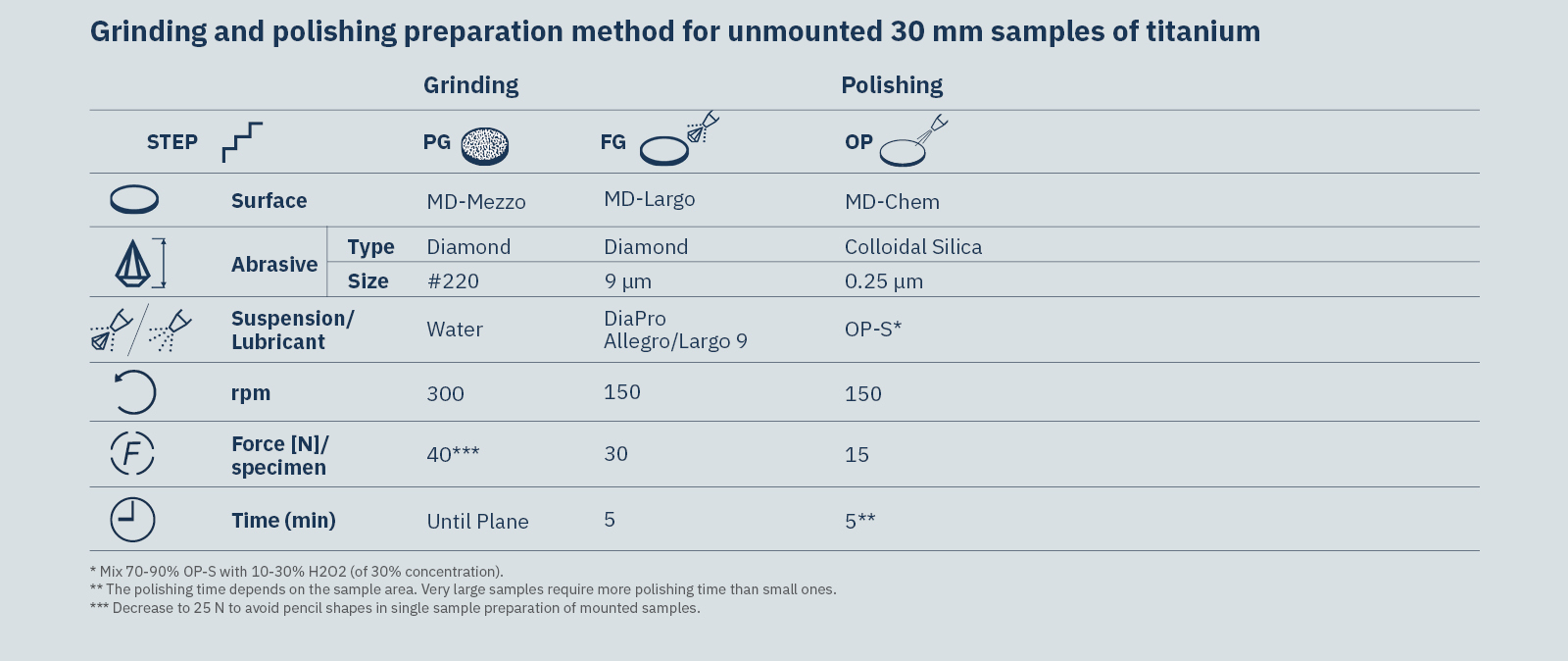
Tabelle 2. Präparationsmethoden zum Schleifen und Polieren von nicht eingebetteten 30-mm-Proben aus Titan.
Detaillierte Beschreibungen und bewährte Methoden zum Polieren, Elektropolieren und Ätzen von mit Titan additiv gefertigten Proben finden Sie in der vollständigen Application Note.
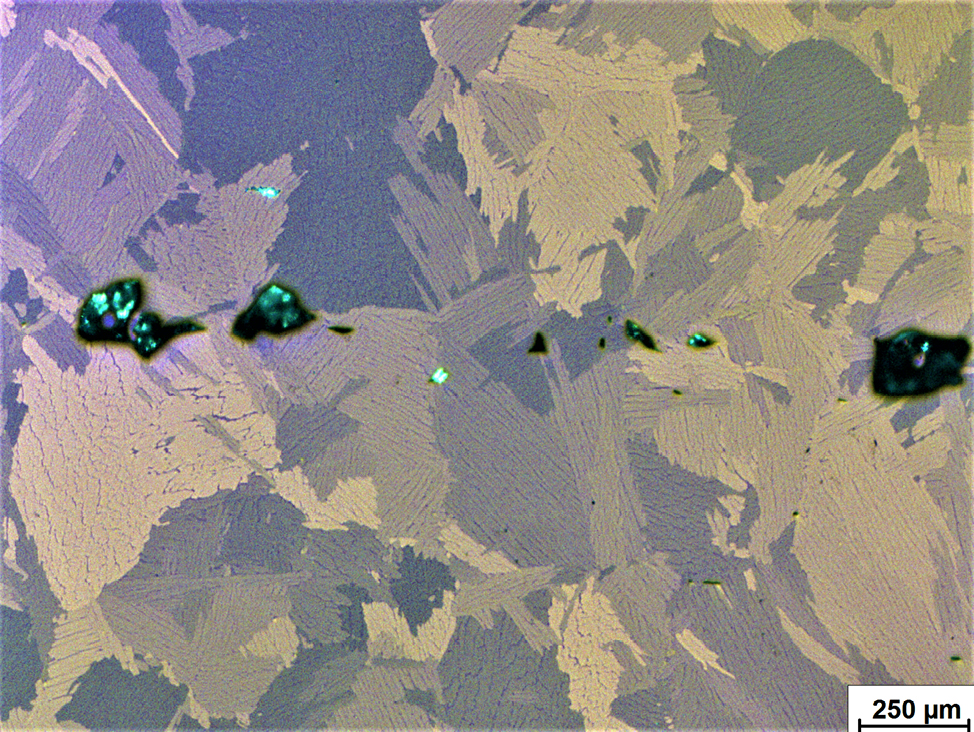
Abb. 14. Endpolierte Titanprobe mit Poren. Poliert mit MD-Chem mit OP-S NonDry und Zusatzmittel, mit sichtbarem Gefüge im Polarisationskontrast.
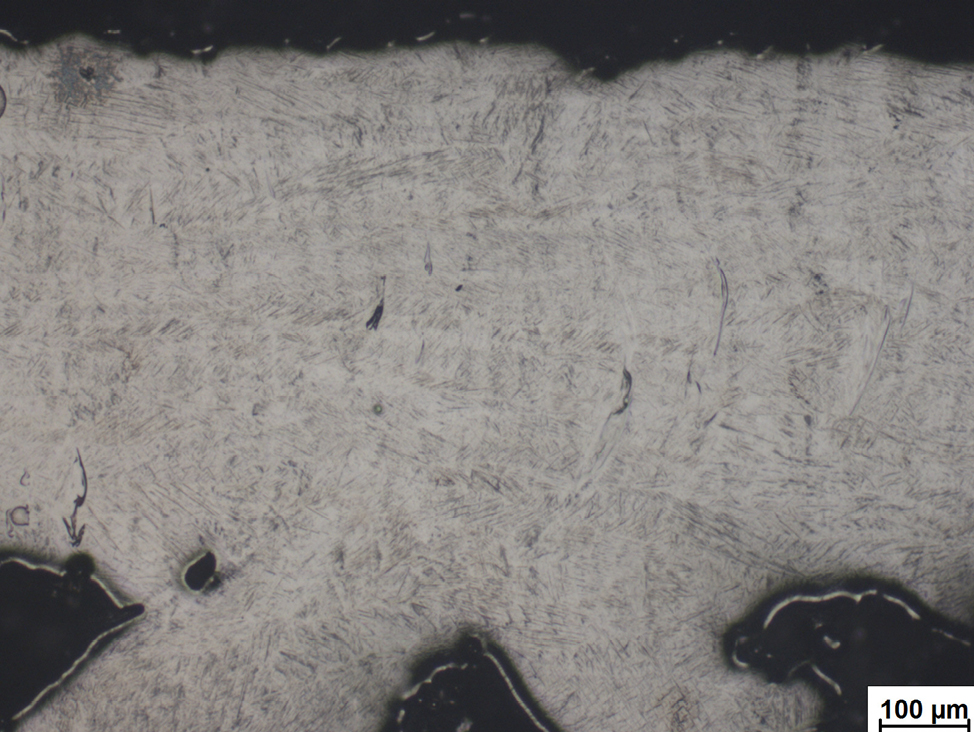
Abb. 15. Titanlegierung. Elektrolytische Präparation mit A3, nicht eingebettet. Hellfeld.

Abb. 16. Titanlegierung. Eektrolytisch poliert und chemisch geätzt mit Ätzmittel nach Fuss. Hellfeld.
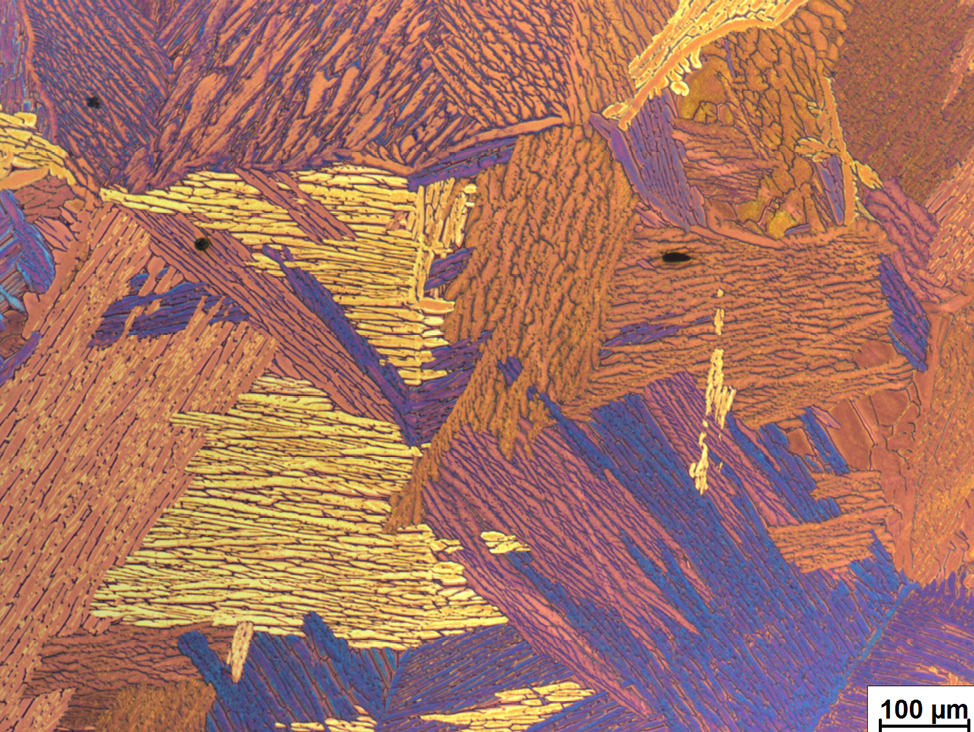
Abb. 17. Titanlegierung nach dem Ätzen mit Ätzmittel nach Keller. Polarisiertes Licht. Aluminium Obwohl Aluminium weich ist, können Legierungselemente seine mechanischen Eigenschaften erheblich verändern. In der Regel sollte die Präparation additiv hergestellter Proben den Methoden folgen, die für ähnliche Aluminiumproben verwendet werden.
- Zur Vermeidung von Verformungen, Kratzerbildung und Kantenabrundung wird die Verwendung einer starren Planschleiffläche empfohlen, die speziell für Aluminiumlegierungen entwickelt wurde und als MD-Molto bezeichnet wird.
- Beim Feinschleifen eignet sich MD-Largo mit Diamantsuspension (z. B. DiaPro Allegro/Largo) für viele Arten von Aluminium.
- Um ein sorgfältiges Polieren zu gewährleisten, folgt nach dem Feinschleifen ein Diamantpolierschritt (MD-Mol) und ein Oxidpolierschritt (kolloidales Siliziumdioxid, OP-U).
- Um mehr oder spezifischere Details sichtbar zu machen können chemische, elektrochemische und optische Ätzverfahren oder eine Kombination davon verwendet werden.
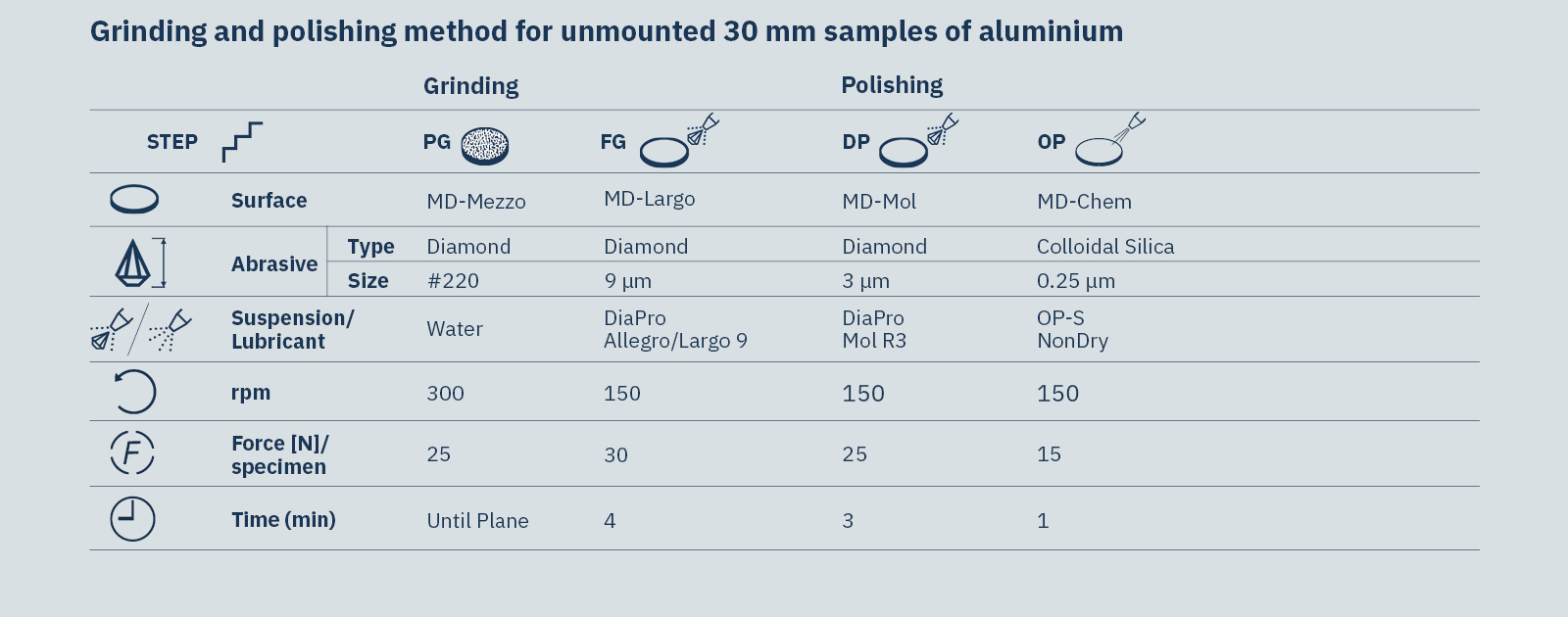
Tabelle 3. Methode zum Schleifen und Polieren von 30-mm-Proben aus Aluminium
Ausführlichere Informationen und Methoden finden Sie in der vollständigen Application Note.
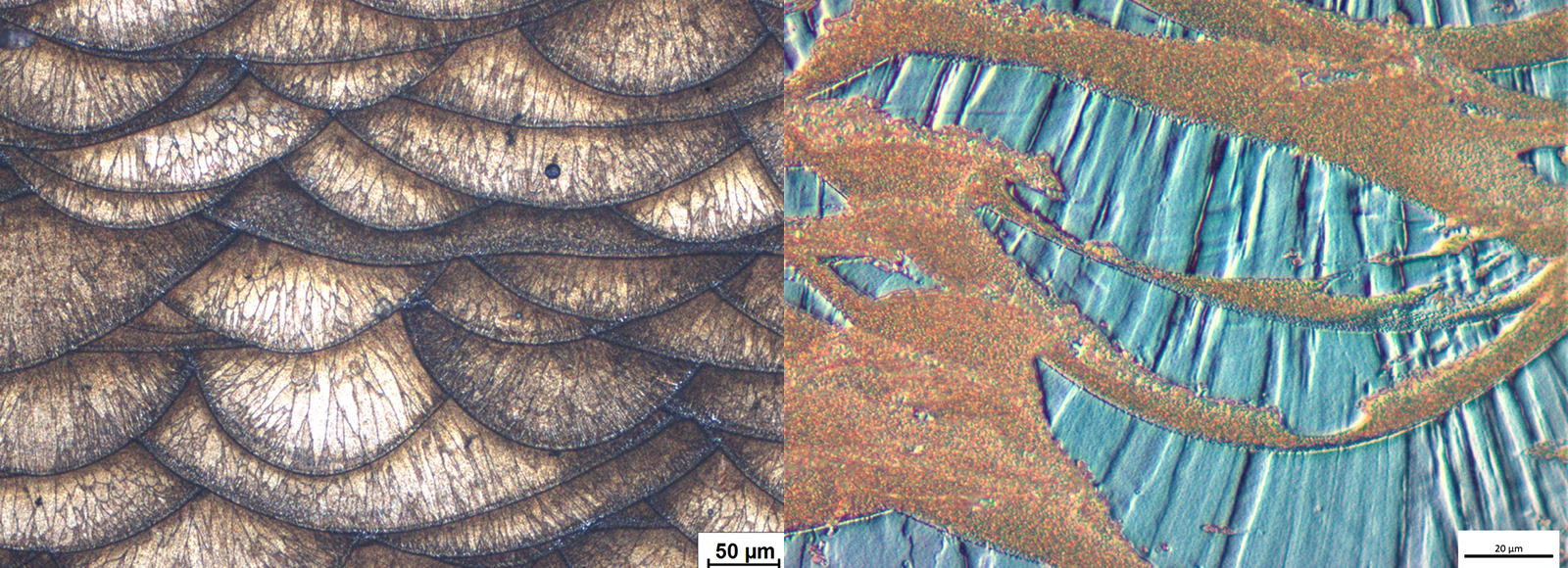
Abb. 18. Unterschiedliche Aluminiumlegierungen nach dem Ätzen nach Barker im Hellfeld (links) und Differenzialinterferenzkontrast DIC (rechts).
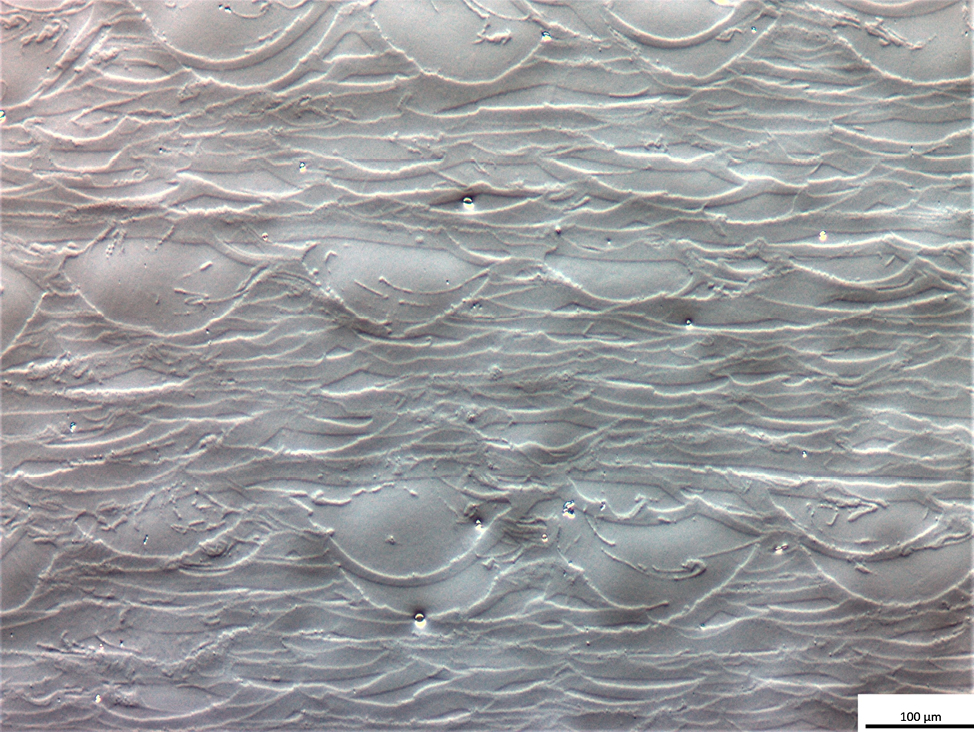
Abb. 19. Endpolierte Oberfläche einer Aluminiumlegierung; Mit MD-Chem und OP-S poliert. Differentialinterferenzkontrast, DIC, ungeätzt.
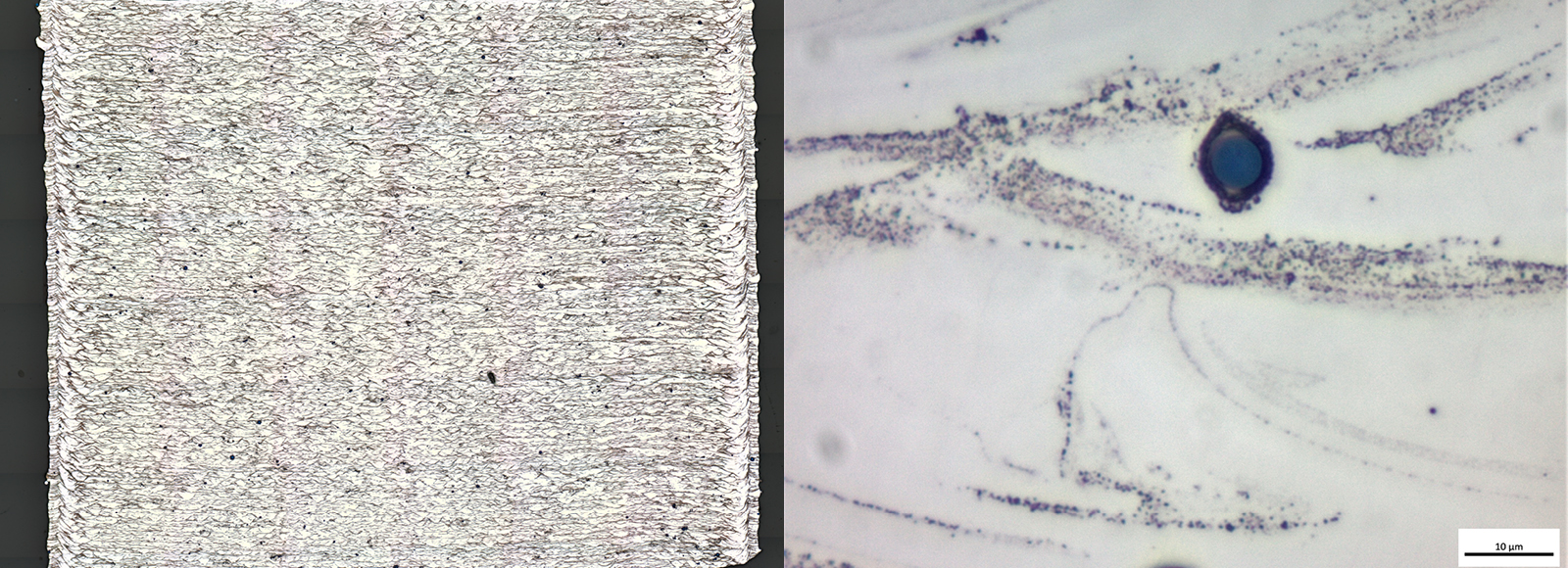
Abb. 21. Übersicht über die Aluminiumlegierung, geätzt nach Barker (links). Detail der Aluminiumlegierung mit Niederschlag bei starker Vergrößerung (rechts). Hellfeld.
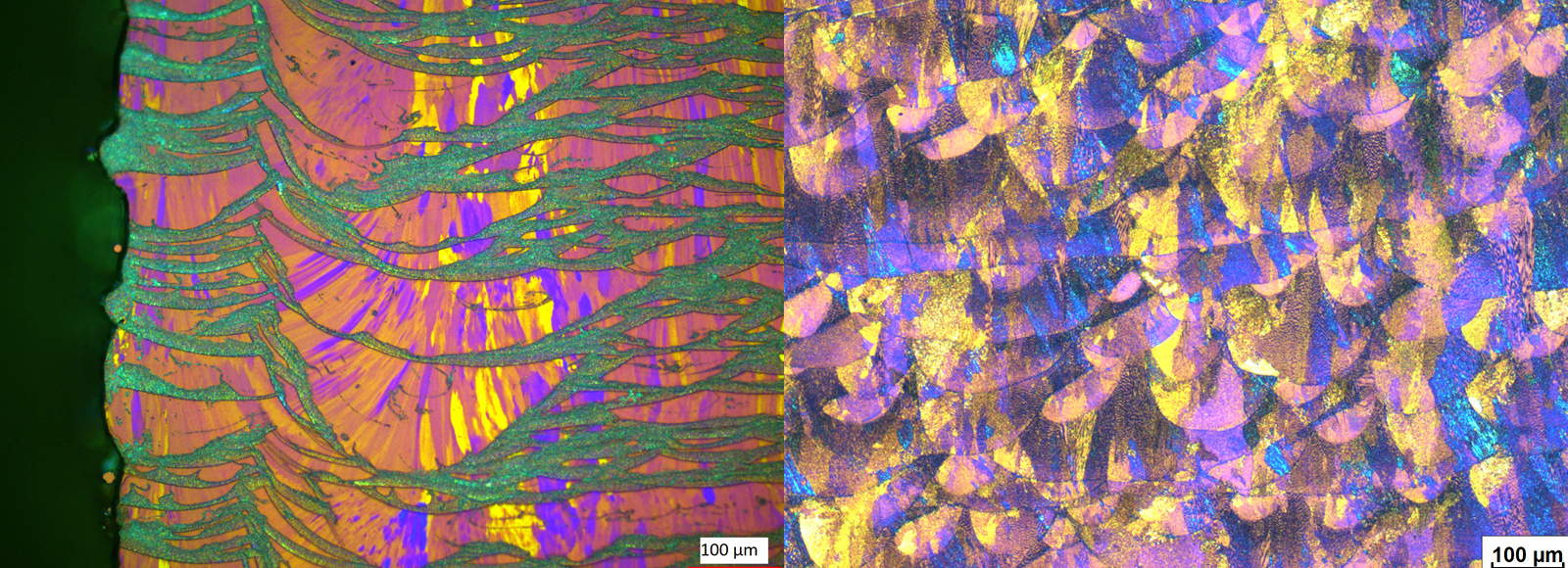
Abb. 22. Aluminiumlegierung nach Ätzen nach Barker (links). Inconel, geätzt nach Adler (rechts). Polarisiertes Licht. Edelstahl und Legierungen auf Nickelbasis Da diese Materialien oft weich und duktil sind, sind sehr grobe Schleifunterlagen und hoher Druck zu vermeiden. In der Regel sollte die Präparation den Standardmethoden für andere Edelstähle und Legierungen auf Nickelbasis folgen.
- Verwenden Sie eine spezielle Planschleifscheibe, z. B. MD-Alto.
- Beim Feinschleifen wird eine Diamantsuspension auf einer starren Scheibe (MD-Largo) oder MD-Plan-Tuch verwendet.
- Nach dem Feinschleifen folgt ein sorgfältiges Diamantpolieren mit einem mittelharten/harten Tuch (MD-Dac).
- Wir empfehlen ein Endpolieren mit kolloidalem Siliziumdioxid (OP-S) oder Aluminiumoxid (OP-A), um feine Kratzer zu entfernen.
- Elektrolytisches Ätzen mit 10 % Oxalsäure in Wasser ist üblich. Bei Duplexstählen liefert das elektrolytische Ätzen mit NaOH (20 % in Wasser) jedoch bessere Ergebnisse.
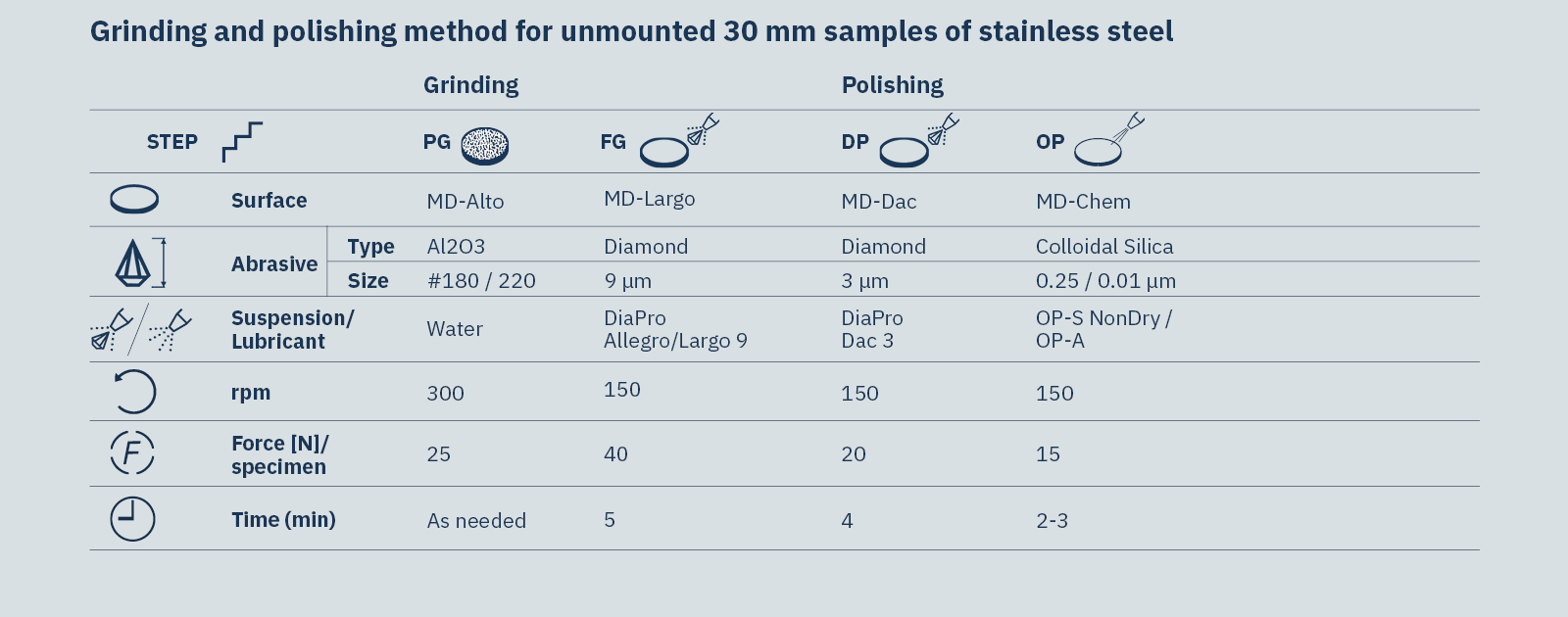
Tabelle 4. Methode zum Schleifen und Polieren von Proben aus Edelstahl
Ausführlichere Informationen und Methoden, einschließlich der Präparation von Proben für die Porositätsbewertung, finden Sie in der vollständigen Application Note.
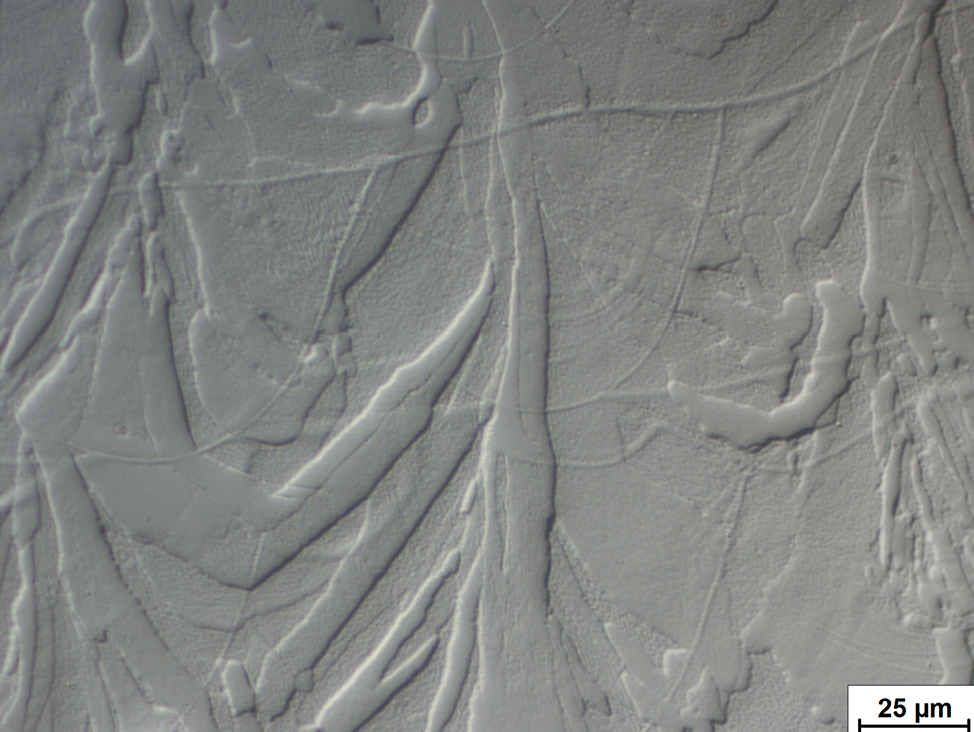
Abb. 24. Austenitischer Stahl nach dem Polieren mit OP-S auf MD-Chem. Gefüge ohne chemisches Ätzen sichtbar. Differentialinterferenzkontrast, DIC.
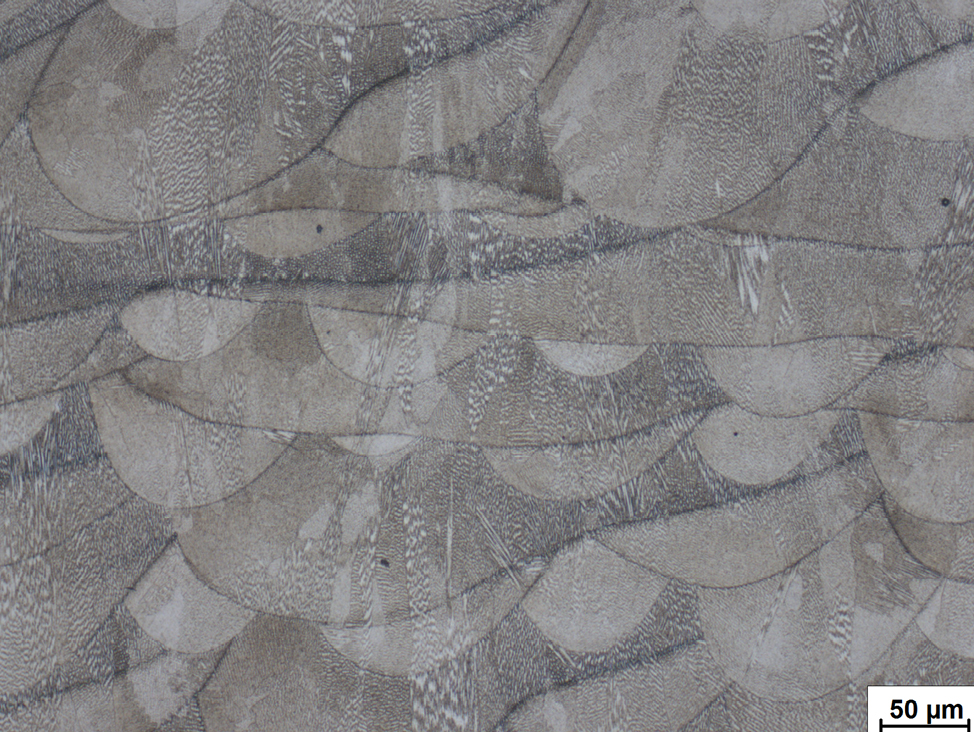
Abb. 25. Inconel 718, geätzt mit Ätzmittel nach Adler. Hellfeld.
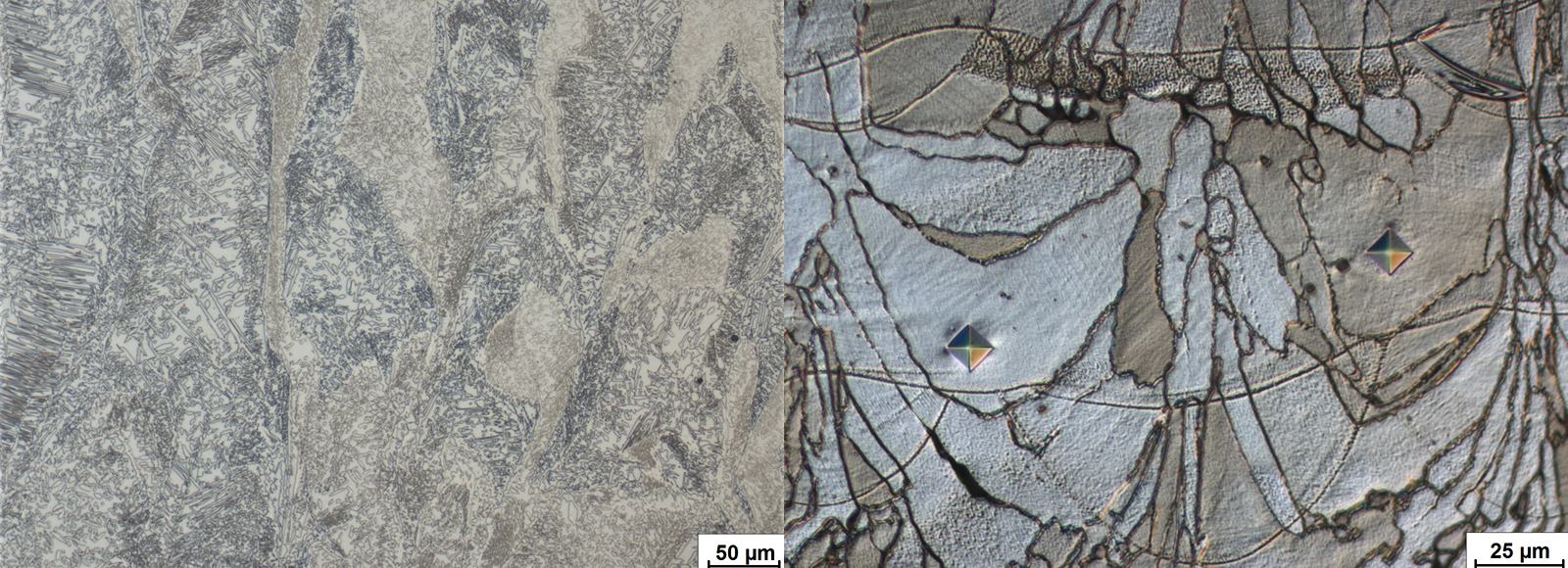
Abb. 26. Duplexstahl 1.4462 nach elektrolytischem Ätzen mit Oxalsäure (10 %). Hellfeld (links). Duplexstahl 1.4410 mit Mikrohärteeindrücken, nach elektrolytischem Ätzen mit 20 % NaOH in Wasser. Differentialinterferenzkontrast, DIC (rechts). Werkzeugstähle Werkzeugstahl ist ein Stahl mit einem hohen Anteil an Legierungselementen, wie Chrom, Nickel, Vanadium oder Molybdän. Die größte Herausforderung beim Schleifen und Polieren ist der Erhalt von Karbiden und nichtmetallischen Einschlüssen. In der Regel sollte die Präparation den Standardmethoden folgen, die für andere Werkzeugstähle verwendet werden.
- Zum Planschleifen wird die Verwendung von Planschleifscheiben mit eingebetteten Diamanten (MD-Piano) empfohlen.
- Verwenden Sie zum Feinschleifen eine metallgebundene Feinschleifscheibe (MD-Allegro) mit Diamantsuspension.
- Für hochlegierte Stähle kann Klemm-Ätzmittel verwendet werden.
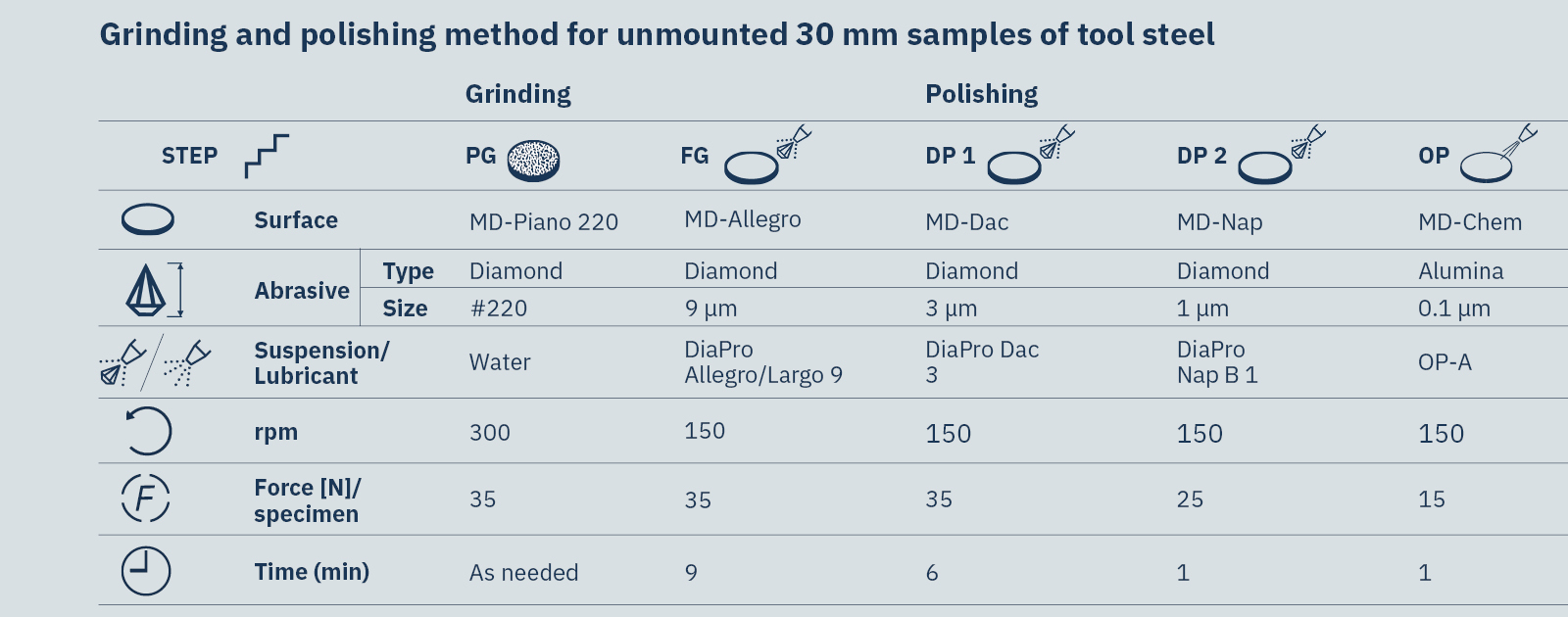
Tabelle 5. Schleif- und Poliermethode für 30-mm-Proben aus Werkzeugstahl.
Weitere Informationen und Methoden finden Sie in der vollständigen Application Note.
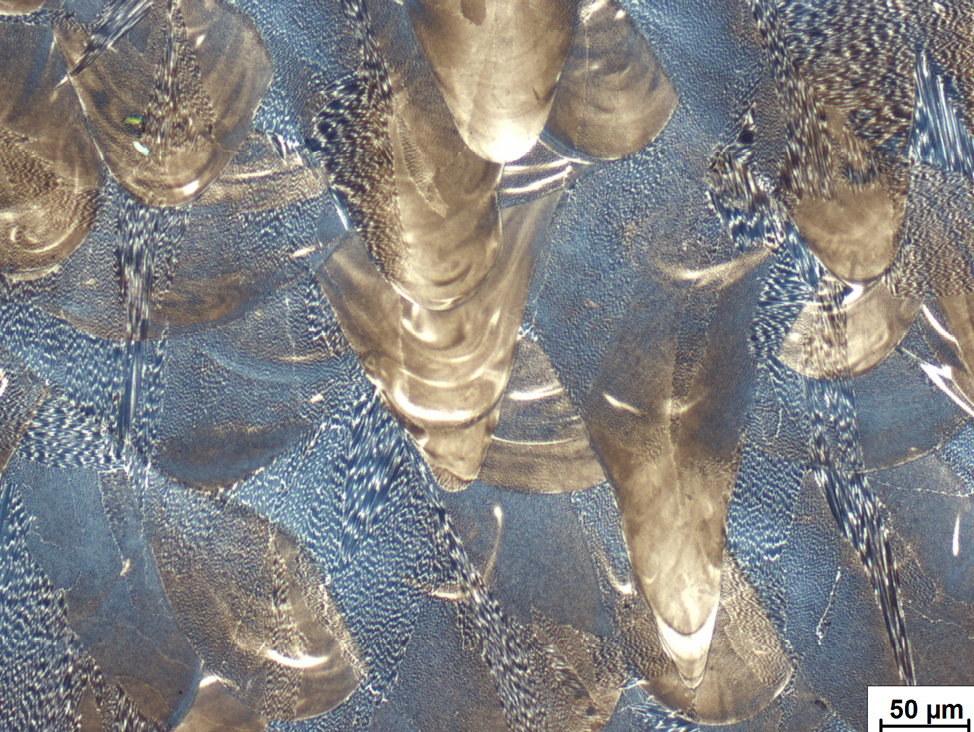
Abb. 27. Werkzeugstahl 1.2709 nach Ätzen mit modifizierter Klemm (10/3) und Zugabe von HCl. Weitere Informationen